Join Workshops
Physical Address
304 North Cardinal St.
Dorchester Center, MA 02124
How Does a Water Chiller Help in Laser Cutting?
A water chiller uses a water cooling mechanism inside the laser machine to control the heat and protect material that affects finer precision.
Laser cutting and engraving are precise and intricate processes, often involving high heat generation that can impact the laser machine’s quality and longevity.
One critical component in managing this heat is a cooling system, and water cooling is so far the most popular method.
This article will explore how these cooling systems work, their benefits, and why they are essential for efficient laser cutting and engraving.
Key Takeaways:
- Purpose of Cooling Systems: Control the temperature of the laser machine.
- Benefits: Enhanced precision, extended machine lifespan, and reduced maintenance.
- Types: Industrial chillers, portable units, and laser-specific coolers.
- Usage Tips: Regular maintenance and proper setup to ensure optimal performance.
What is a water Cooling System and How Does It Work?
A cooling system removes heat from the laser cutting and engraving machine, ensuring it operates optimally.
A water cooler circulates chilled water through the laser setup, absorbing the excess heat generated during operation. This process prevents overheating and maintains consistent performance, especially protect the material from overburning.
Research from the Journal of Manufacturing Processes highlights that maintaining a stable temperature is crucial for achieving high-quality cuts and engravings. The study found that machines equipped with efficient cooling systems produced significantly more precise results compared to those without such systems.
Why is Temperature Control Crucial in Laser Cutting and Engraving?
Temperature control is vital in laser cutting and engraving for several reasons such as maximizing the longevity of the laser, ensuring laser precision, and protecting the material from any damage.
High temperatures can distort the laser beam, leading to reduced precision and inconsistent cuts. High temperature can also reduce the lifespan of CO2 laser tube in some cases.
Overheating can also cause significant wear and tear on the machine, decreasing its lifespan and increasing maintenance costs. By maintaining a stable temperature, cooling systems help achieve high-quality results and extend the machine’s operational life.
For example, a study published in the International Journal of Advanced Manufacturing Technology found that temperature fluctuations of just a few degrees could lead to significant deviations in cut quality. The study also noted that consistent temperature control could extend the operational life of laser machines by up to 50%.
What Are the Benefits of Using a Cooling System?
In a nutshell, the key benefits of using a water cooling method in laser engraving involves improved precision, maximized machine lifespan, reduced risk of material damage and lower machine maintenance.
Improved Precision
A stable temperature ensures that the laser beam remains consistent, resulting in precise cuts and engravings.
For example, if you are using a CO2 laser machine, equipped with water cooling, your laser precision would remain the same as mentioned. However, laser engraver without cooling mechanism will always bear the risk of precision distortion.
A research paper from the Journal of Materials Processing Technology demonstrated that laser engravers with effective cooling systems achieved up to 20% more accurate engravings compared to those without.
Extended Machine Lifespan
Heat is a major factor in the wear and tear of laser machines. A cooling unit mitigates this by keeping the machine cool, thereby reducing the likelihood of component failure and extending the overall lifespan of the equipment.
According to a report by the American Society of Mechanical Engineers, machines with integrated cooling systems can operate efficiently for up to twice as long as those without, significantly reducing the need for costly replacements.
Less Material Damage
A water chiller effectively helps protect materials from damage. For instance, if you are engraving leather, or etching glasses with your laser machine, a water cooling mechanism will control the inner temperature and protect such heat sensitive materials from getting melted and over-burn.
Reduced Maintenance
Machines that overheat frequently require more maintenance. Cooling systems help maintain a constant temperature, reducing the need for frequent repairs and downtime. According to a study by the Laser Institute of America, consistent cooling can decrease maintenance costs by up to 30%.
A practical example is seen in the aerospace industry, where companies like Boeing have reported a marked reduction in maintenance frequency and costs due to the implementation of advanced cooling systems in their laser cutting equipment.
What Happens If Your Laser Machine Does Not Have Any Cooling System?
Operating a laser machine without proper cooling can lead to several detrimental effects including overheating, reduced precision and heavy maintenance.
Without a cooling unit, the machine is likely to overheat quickly. This can cause the laser components to malfunction or shut down, leading to interruptions in your work.
Excessive heat can distort the laser beam, resulting in inaccurate cuts and engravings. This compromises the quality of your projects and increases material wastage.
Heat accelerates the wear and tear on various machine components, leading to more frequent breakdowns and a shorter lifespan for the laser machine.
Without cooling, the machine will require more frequent repairs and maintenance. The increased strain on components can lead to costly replacements and downtime.
Ensuring your laser machine is equipped with a reliable cooling method is essential to prevent these issues and maintain efficient operation. However, if you are using diode lasers, you may use air assist that alters the need of water cooling to some extent.
What Types of Cooling Systems Are Available?
There are several types of cooling systems designed for laser machines, each catering to different needs. However, most modern laser machines such xTool P2, OMTEch Polar and Gweike Cloud has water cooling in built.
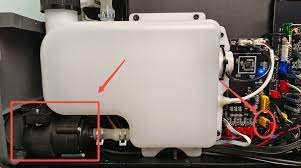
1. Industrial Chillers: These are large, robust units suitable for heavy-duty laser cutting and engraving operations. They offer high cooling capacity and are ideal for industrial settings.
For example, an industrial chiller used in automotive manufacturing can cool multiple laser machines simultaneously, ensuring consistent performance across the production line.
2. Portable Cooling Units: Portable units are smaller and more versatile, making them suitable for various environments, including small workshops and hobbyist setups.
An example would be a portable cooler used in a small jewelry engraving shop, providing adequate cooling for intricate designs without the need for a large, stationary unit.
3. Laser-Specific Coolers: These chillers are specifically designed for laser machines, offering tailored cooling solutions that match the specific requirements of different laser systems. Check if your CO2 laser machine contains water cooling. SO far we know, only the Glowforge and some low quality Chinese laser machine does not offer water cooling.
How to Protect Your Laser Engraver If There Is No Cooling Method Available
If a cooling system is not available, there are several alternative methods such as using air assist, applying masking tape, controlling laser power and regular monitoring can help you protect your laser engraver from overheating:
Use Air Cooling Systems
Air cooling systems use fans to dissipate heat. Although less efficient than water-based units, they can provide adequate cooling for smaller laser machines. In laser cutting, we call them air assist.
A study from the Applied Thermal Engineering journal indicates that air cooling can reduce operating temperatures by up to 10 degrees Celsius, which is sufficient for low-intensity laser tasks.
Operate in Short Bursts
To prevent overheating, operate the laser engraver in short bursts and allow the machine to cool down between sessions. This method reduces continuous heat buildup.
For example, a hobbyist using a laser engraver for crafting can schedule breaks after every 15 minutes of operation to prevent overheating.
Ensure Proper Ventilation
Place the laser machine in a well-ventilated area. Good airflow helps dissipate heat more effectively, reducing the risk of overheating.
For the enclosed laser engravers, it gets tougher to ensure ventilation unless there are exhaust system.
Use Heat Sinks
Heat sinks are passive cooling devices that absorb and dissipate heat from the laser components.
They can be an effective solution to manage heat in the absence of active cooling systems.
You do not need heat sinks unless you are operating a large industrial laser machine without a proper cooling system.
Monitor and Ensure Maintenance
Install temperature sensors to monitor the machine’s temperature continuously. If the temperature rises above safe levels, pause the operation to allow the machine to cool down.
Keep the machine clean and free of dust and debris, which can insulate heat. Regular maintenance ensures that the cooling mechanisms in place are functioning correctly.
How can you install a water chiller in your laser cutter?
Choose the Appropriate Chiller: Ensure the water chiller you select matches your laser engraver’s requirements. Check its capacity, cooling power, and dimensions, and make sure it aligns with the manufacturer’s specifications for optimal performance.
Prepare the Area: Placing a water chiller inside of your laser machine is not possible if you are upgrading your old laser cutter with a water cooling mechanism. You need to clear a spot near your laser engraver for the chiller. This space should have good ventilation and be easily accessible. Place the chiller on a stable surface, ideally close to the engraver for easy connection.
Connect the Inlet and Outlet: Identify the water inlet and outlet ports on both your laser engraver and the chiller. Use appropriate hoses or tubing to connect them securely, ensuring there are no leaks.
Power Up the Chiller: After making the connections, switch on the water chiller. Set the desired temperature and flow rate according to your engraving needs. Follow the manufacturer’s guidelines for proper operation and maintenance.
Monitor and Adjust: During use, regularly check the chiller’s temperature and flow indicators. Adjust as necessary to maintain optimal cooling. Routinely inspect for leaks or malfunctions and address any issues promptly to avoid damage to your engraver.
How to Maintain Your Water Chiller for Optimal Performance?
Regular maintenance of your cooling system is essential to ensure its efficiency and longevity. Here are some tips:
- Regular Cleaning: Clean the cooling system regularly to prevent the buildup of debris and contaminants.
- Monitor Water Levels: Ensure that the water levels are adequate and top up as necessary.
- Check for Leaks: Regularly inspect the system for any signs of leaks or damage.
- Replace Filters: Change the filters periodically to maintain water purity and optimal cooling performance.
Cooling systems play a crucial role in the efficiency and effectiveness of laser cutting and engraving.
By maintaining a stable temperature, they ensure precise cuts, extend the lifespan of the machine, and reduce maintenance needs. Investing in a high-quality cooling system is a wise decision for anyone looking to optimize their laser operations.
For more detailed advice on selecting and maintaining a cooling system, consult with industry experts or refer to authoritative sources.
If you want to learn laser engraving and be an expert in this field, book CraftEtch’s training and workshops.